Beautiful Blacktop: Asphalt Maintenance and Repair for Self-Storage Facilities
While self-storage operators commonly examine their roofs, buildings and unit doors, they also need to pay regular attention to their asphalt. Properly maintaining your driving surfaces is integral to facility curb appeal and safety. Learn to care for them and expand their lifespan.
September 23, 2023
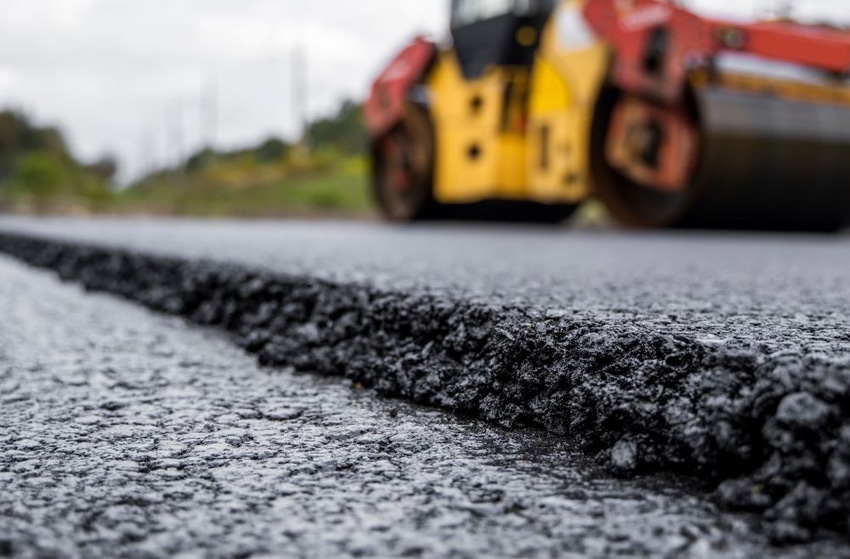
Self-storage facilities rely on well-maintained infrastructure to ensure smooth performance and attract customers. Among the critical components of these properties are the asphalt drives and walkways that support vehicle and foot traffic. Not only do these surfaces form the foundation for operational efficiency, they directly impact curb appeal, influencing customers’ first impressions of the business.
Caring for your pavement isn’t only essential for aesthetics but to ensure site safety and functionality. Consistent maintenance mitigates cracks and potholes, ensuring an easily accessible environment for tenants and employees. Overlooking this important element can lead to substantial expenses for repairs. It might even lead to liability for loss or injury.
Let’s explore strategies to extend the lifespan of your asphalt. I’ll address common maintenance and repairs, plus ways to reduce replacement costs without compromising quality.
Pavement before and after full-depth reclamation (FDR)
Maintenance Strategies
Extending the life of your asphalt surfaces starts with being proactive in routine maintenance. One of the best protections is a treatment called sealcoating. Asphalt is porous and can be penetrated by water, which leads to degradation from below. Minimizing absorption is critical, especially in climates that experience significant and frequent freezing and thawing in the winter months. As water freezes, it expands, causing cracks. Sealcoat serves as a barrier, safeguarding the asphalt from elements like water, UV rays and chemicals, thus mitigating deterioration.
Another option for self-storage asphalt maintenance is a treatment called road slurry, often referred to as slurry seal. This is similar to sealcoat in that it helps protect the surface, but slurry contains aggregate and sand, making it thicker to apply. The aggregate provides texture that enhances traction and skid resistance. Road slurry is more common in areas with long seasons of ice and snow. Just be aware that this product is more expensive than sealcoat. In fact, it doesn't become cost-effective until you apply 100,000 square feet or more.
The frequency of application for seal or slurry can vary based on several factors, including climate, traffic volume and the quality of the initial pavement installation. The general guideline is that asphalt surfaces should be treated every three to five years. Also, keep in mind that neither solution is a substitute for addressing underlying structural issues. They should instead be part of a comprehensive maintenance plan that includes periodic inspections.
Repair Methods
Well-maintained asphalt will typically last 15 to 20 years before it needs major repairs or replacement. You certainly may face the latter if your self-storage facility is aging. The good news is, depending on the severity of the deterioration, there are ways to keep costs down and achieve long-lasting, quality pavement. Following are three to consider.
Mill and inlay. This common process is used to restore the structural integrity, functionality and appearance of surfaces that have experienced wear or damage over time. Milling involves removing a layer of existing asphalt, then clearing the remaining surface of debris, dust and loose material. A tack coat is then applied to ensure proper adhesion between the existing pavement and a new layer of hot-mix asphalt, known as an inlay. This method can be especially cost-effective when paving fabric or geotextiles are found in the existing pavement.
Paving fabric is used between layers of asphalt, but disposing of it properly can be costly in some areas. You can possibly avoid having to remove it during the mill and inlay process by staying above the fabric layer; however, if the previous overlay is one inch or less, you may not have a choice.
(Above left) A paving machine adding 3 inches of new asphalt during the mill and inlay process. (Above right) Pavement after the mill and inlay.
Fiber-reinforced asphalt. This mixture incorporates various types of fibers during the production process to enhance pavement performance and durability. The fibers can be made from materials like glass, polyester, polypropylene, Kevlar or natural sources. This process is part of the broader trend of using innovative materials and techniques to improve sustainability. It offers a solution to common pavement concerns while extending product life. Ultimately, it reduces maintenance costs and ensures safer and more durable paved environments.
Using fiber-reinforced asphalt in a mill-and-inlay application can extend the life of your self-storage pavement by seven to 10 years and reduce reflective cracking. However, it isn’t cost-effective when paving less than 25,000 square feet.
Full-depth reclamation (FDR). This is an innovative way to replace asphalt while optimizing resources and minimizing waste. The process can be a good option if full-depth removal and replacement is necessary.
Mixing the pulverized asphalt with cement powder during the FDR process
FDR entails specialized equipment to pulverize the existing asphalt, breaking it down into small particles and mixing it with the subgrade. In severe situations, a stabilizing agent (typically cement or lime) is blended in. This forms a chemical reaction that strengthens the pavement, enhancing its load-bearing capacity and contributing to a durable and resilient surface that can withstand heavy traffic and changing weather conditions. This method recycles existing materials, reducing the need for extensive excavation and disposal. It also reduces the overall cost and the environmental impact.
Understanding the various options for self-storage pavement maintenance and rehabilitation is essential for making informed decisions that balance cost, longevity and sustainability. While well-maintained surfaces can last 15 to 20 years before requiring major repair or replacement, there are ways to significantly extend this life, sometimes by another 10 to 20 years! Paying close attention to facility asphalt can save you money while enhancing curb appeal.
Scott Jolly is co-owner of Site Consulting Specialists, a provider of project management, engineering, asphalt and concrete, and roofing services. He combines his real estate experience with concrete and paving expertise to create savings for large portfolio owners. As an investor, he understands the impact capital expenditures can have on a business net operating income and investor returns. For more information, email [email protected].
About the Author(s)
You May Also Like